ПРИМЕНЕНИЕ ПЕНЫ ДЛЯ ПОЛУЧЕНИЯ ТЕПЛОИЗОЛЯЦИОННОГО ПЕРЛИТОЦЕМЕНТА
ПРИМЕНЕНИЕ ПЕНЫ ДЛЯ ПОЛУЧЕНИЯ ТЕПЛОИЗОЛЯЦИОННОГО ПЕРЛИТОЦЕМЕНТА
Аннотация
Приведены результаты исследований по разработке составов и исследованию физико-механических свойств теплоизоляционного перлитоцемента. При проектировании состава перлитоцемента исходили из того, что основными компонентами, влияющими на плотность, являются вспученный перлитовый песок и цемент. Установлено, что применение пены позволяет резко увеличить объем цементного теста, что обеспечивает возможность перемешивания раствора с хрупкими, слабопрочными зернами вспученного перлитового песка. В результате экспериментальных исследований с регулированием соотношения «вспученный перлитовый песок-цемент» получен особо легкий материал со средней плотностью в сухом состоянии 150-200 кг/м3, прочностью на сжатие 0,32-0,43 МПа, коэффициентом теплопроводности 0,048-0,052 Вт/(м·°С)
1. Введение
Сегодня в Казахстане, как и во всем мире, проблемам энерго- и теплосбережения придается все большее значение, что связано не только с экономическими потребностями, но и экологическими. Физической величиной, характеризующей способность ограждающей конструкции к теплопередаче, является приведенное сопротивление теплопередаче (R0), которое следует принимать в соответствии с заданием на проектирование, но не менее требуемых значений Rтр0 определяемое исходя из санитарно-гигиенических и комфортных условий и условий энергосбережения по данным, приведенных в Строительных правилах Республики Казахстан .
Для условий городов Алматы и Астана термическое сопротивление ограждающих конструкций, вычисленное авторами статьи должно быть соответственно, не менее 2,675 и 3,5 (м2·°С)/Вт. Для сравнения: термическое сопротивление стен для условий г. Москвы составляет 3,2, а для всей территории Германии – 4,166 (м2·°С)/Вт. Как видим, несмотря на более мягкий климат, в Германии требования к теплозащите стен значительно выше, чем в РК и России.
При действии старых норм в РК (до 2001 г.) применение современных высокоэффективных в теплотехническом отношении материалов было не обязательным. Так, например, в г. Алматы кирпичные дома строили толщиной стены на два с половиной кирпича (62,5 см), а в панельных домах изоляционным слоем служил керамзитобетон плотностью 1000 кг/м3 толщиной 17 см, несущим слоем – тяжелый железобетон толщиной 15 см и отделочный слой изготавливался из раствора толщиной 3 см. Согласно проведенным расчетам термическое сопротивление кирпичной и бетонной стены указанных конструкций составляет соответственно 0,893 и 0,632 (м2·°С)/Вт, что соответственно в 3 и 4,2 раза меньше современных норм по теплозащите наружных конструкций зданий, принятых в 2001 г.
Согласно расчетам авторов статьи, какая толщина стены в г. Алматы, в случае его возведения из традиционных стеновых материалов, должна быть в настоящее время видно из рис. 1. Значения плотностей материалов, приведенных на рис. 1 следующие: полнотелого кирпича – 1800 кг/м3; пустотного кирпича – 1000 кг/м3; керамзитобетона – 1000 кг/м3; автоклавного газобетонного блока – 500 кг/м3; перлитобетонного блока – 600 кг/м3; базальтовой плиты – 80-125 кг/м3; пенополистирола – 20-25 кг/м3.
Известно, что наружные ограждающие конструкции должны быть многослойными с применением теплоизоляционных материалов. В качестве исключения можно изготавливать однослойные стены из ячеистобетонных блоков, но при этом толщина стены с учетом защитного отделочного слоя все равно будет больше 60 см, что для многоэтажных зданий неприемлемо из-за значительной потери полезной площади. С другой стороны, при строительстве в сейсмической зоне, такая стена также не целесообразна, не говоря о том, что на такую стену невозможно навесить предметы мебели, радиаторы отопления и прочие предметы быта.
В строительстве Казахстана получила распространение навесная фасадная конструкция наружной стены, предусматривающая кладку из автоклавных газобетонных блоков толщиной 20 см, изоляционный слой из базальтовой плиты марки П80, П100 толщиной 10 см и навесные фасадные плиты. Общая толщина стены при этом не превышает 35 см.
Таким образом, можно заключить, что на сегодняшний день без применения теплоизоляционных материалов, невозможно получить разрешение на строительство жилых зданий и сооружений. Также известно, что только два вида промышленно производимых материалов могут быть успешно использованы в качестве теплоизоляторов: это пенопласты и минераловатные (базальтовые) изделия. Действительно, в последние годы в строительстве Республики Казахстан и других странах СНГ в качестве теплоизоляционных материалов используются именно минераловатные и пенопластовые изделия.
При высокой теплоизолирующей способности, минераловатным плитам и пенопластам все же присущи два неблагоприятных аспекта: первый – это скрытая опасность, которая может проявиться в период эксплуатации жилых зданий, а конкретно – экологическая небезопасность для жильцов квартир и второй – недолговечность, недостаточная стойкость к пожарам , , , .
Относительно долговечности штукатурного слоя, нанесенного на минераловатные или пенополистирольные плиты, имеются следующие данные. Официально, восемью странами Европы, срок эксплуатации фасадных систем скрепленной теплоизоляции принят равным не менее 25 лет при условиях, что:
- система после выполнения работ прошла сертификацию в независимом органе;
- имеются подтверждения поставки материалов одним поставщиком;
- работы выполнены строго в соответствии с действующим технологическим регламентом;
- система правильно эксплуатируется, то есть через каждые 6-7 лет выполняется расшивка и шпатлевка появившихся трещин, заново окрашивается весь фасад.
Таким образом, серьезность проблемы, связанной с возможностью необходимости ремонта фасадов и теплоизоляционного слоя, построенных и введенных в эксплуатацию жилых и, как правило, частных зданий, которая может возникнуть в ближайшие годы нельзя не учитывать. В России климатические условия значительно более жесткие, чем в Европе, а в Казахстане – резко-континентальный климат, при котором в течение суток температура может изменяться от положительной до отрицательной. В таких условиях европейские нормы, принятые для долговечности теплоизоляционных фасадных систем, требуют изменения и пересмотра с учетом экспериментальных, в том числе и натурных исследований. Так, в работе отмечается, что в Самаре фасадный слой в домах разрушается уже после 3-4-х лет эксплуатации и это приводит к огромным незапланированным затратам на ремонт наружного теплоизоляционного слоя, в то время как в Германии нормативный срок ремонта таких фасадных систем составляет 10 лет. В статье О.А. Лобова и А.И. Ананьева констатируется аварийное состояние фасадных систем с облицованным штукатурным слоем, нанесенным на мягкие утеплители по стекловолокнистой сетке на 5-7-м году эксплуатации домов.
Если с утеплителями из минеральной ваты или пенополистирола знаком каждый строитель, то менее популярные изделия из органического сырья или на основе минеральных компонентов вызывают очень много вопросов. Альтернативой минераловатным теплоизоляционным изделиям, в том числе базальтовым, может стать теплоизоляционный перлитоцемент. Поскольку срок службы у него не ограничен, т.е. будет служить столько же лет, сколько и конструктивная часть здания. Согласно данным японских специалистов, приведенных в монографии немецких ученых, превышает 500 лет . Основными преимуществами теплоизоляции на основе перлитоцемента являются ее огнеупорность, биостойкость и, что очень важно, экологическая чистота.
Сырье для перлитоцемента имеется, так как в городах Алматы и Тараз запущены заводы по выпуску вспученного перлитового песка. Пока они работают на привозном сырье, в частности используют перлитовую породу Арагацкого месторождения (Армения). Но в ближайшей перспективе фирма «ЮНИОН-ПЕРЛИТ» планирует разработку местного месторождения.
Информации о производстве и применении перлитоцементных изделий до настоящего времени в качестве теплоизоляционных материалов для жилых зданий не имеется. В б. СССР, в частности в Российской Федерации, выпускались перлитоцементные полуцилиндры (скорлупы) и плиты, которые применялись для изоляции промышленного оборудования и трубопроводов при температуре изолируемых поверхностей до 600°С . Технология этих изделий отличается сложностью и большой энергоемкостью, что в современных условиях является неконкурентной технологией. Сырьем, кроме вспученного перлитового песка и цемента, является также асбест, который добавляется в большом количестве: в расчете на 1 м3 перлитового песка – 35 кг. Сырьевую смесь готовят в такой последовательности: сначала в растворомешалку заливают воду (на 1 м3 перлита около 850 л воды), затем загружают асбест, засыпают цемент и перлитовый песок. После введения перлита массу перемешивают в течение 1,5 мин и заливают в пресс-форму. Сформованные при удельном давлении 0,05 МПа изделия выталкиваются из формы пресса на перфорированный поддон. Твердение происходит в специальных камерах, где совмещаются пропаривание и сушка. Сначала изделия в течение 4 ч выдерживают при температуре 150°С, затем при температуре 80°С – 6-8 ч, после этого температура резко поднимается до 150°С и изделия высушиваются до остаточной влажности 15-20%.
2. Методы и принципы исследования
При изготовлении пеноперлитоцемента были использованы следующие сырьевые материалы: общестроительный цемент, изготовленный на основе портландцементного клинкера тип І, нормальнотвердеющие (Н), нормальносхватывающиеся, прочностью на сжатие класса 42,5 фирмы «Heidelbergcement» (б. Бухтарминский цементный завод), вспученный перлитовый песок, функциональные добавки и белковый пенообразователь «Биофоам». Физико-механические характеристики использованных сырьевых материалов представлены в табл. 1-3.
Таблица 1 - Физико-механические свойства портландцемента цементного завода фирмы «Heidelbergcement»
Физико-механические показатели | ||||||
остаток на сите 008, % | нормальная густота, % | сроки схватывания, ч-мин | прочность через 28 суток твердения, МПа, при | прочность на сжатие после пропаривания, МПа | ||
начало | конец | изгибе | сжатии | |||
0,8 | 28 | 2-45 | 3-20 | 7,5 | 52,8 | 41,1 |
Таблица 2 - Химико-минералогический состав портландцемента класса 42,5 цементного завода фирмы «Heidelbergcement»
Содержание оксидов, % | Содержание основных минералов | ||||||||
SiO2 | Al2O3 | Fe2O3 | CaO | MgO | SO3 | C3S | C2S | C3A | C4AF |
20,85 | 5,62 | 4,22 | 63,52 | 1,53 | 2,09 | 56,29 | 16,62 | 7,28 | 13,14 |
Таблица 3 - Гранулометрический состав вспученного перлитового песка фирмы ТОО «ЮНИОН-ПЕРЛИТ»
Остатки на ситах, % | ||||||
5 | 2,5 | 1,25 | 0,63 | 0,315 | 0,16 | 0,16< |
- | - | 3,3 | 6,82 | 33,0 | 32,4 | 24,5 |
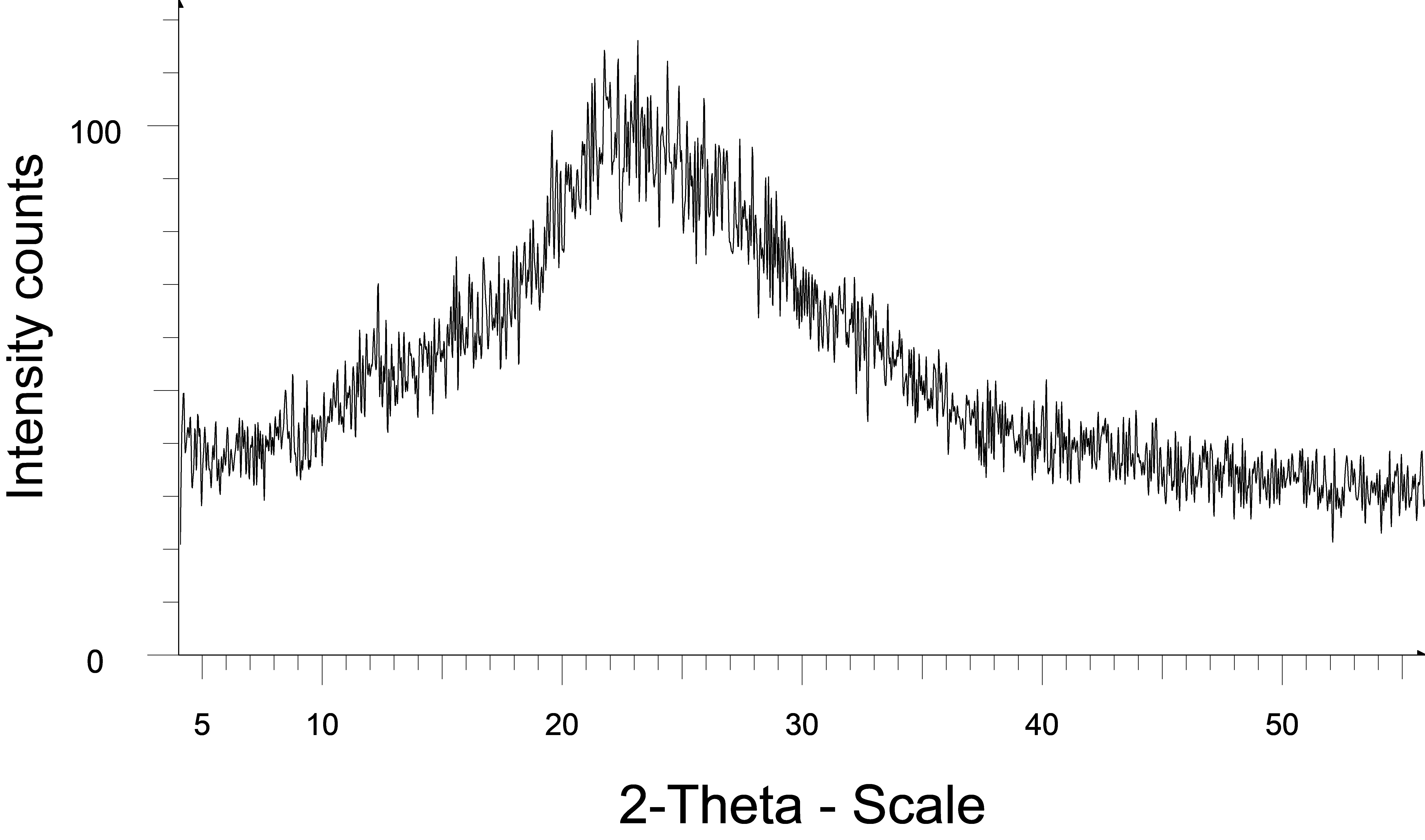
Рисунок 1 - Дифрактограмма вспученного перлитового песка Арагацкого месторождения (Армения)
Насыпная плотность вспученного перлитового песка составляет 60 кг/м3.
Исследования проводились в аккредитованной лаборатории строительных материалов Научно-исследовательского института строительных материалов (НИИ СтромПроект), оснащенной необходимой аппаратурой. Перемешивание сырьевых компонентов осуществляли в мешалках германского и российского производства (рис. 2), пену готовили в емкости объемом 1,5 л в пропеллерной мешалке с регулируемым числом оборотов от 0 до 2000 об/мин (рис. 3), формование производили в формы с внутренними размерами 250х120х100 мм; пропаривание – в лабораторной пропарочной камере, сушку – в лабораторном сушильном шкафу «SNOL 58/350» (58 л, 350°С), испытание на германском прессе «TESTING». Теплопроводность определена с помощью прибора ИТП-МГ4-Зонд.
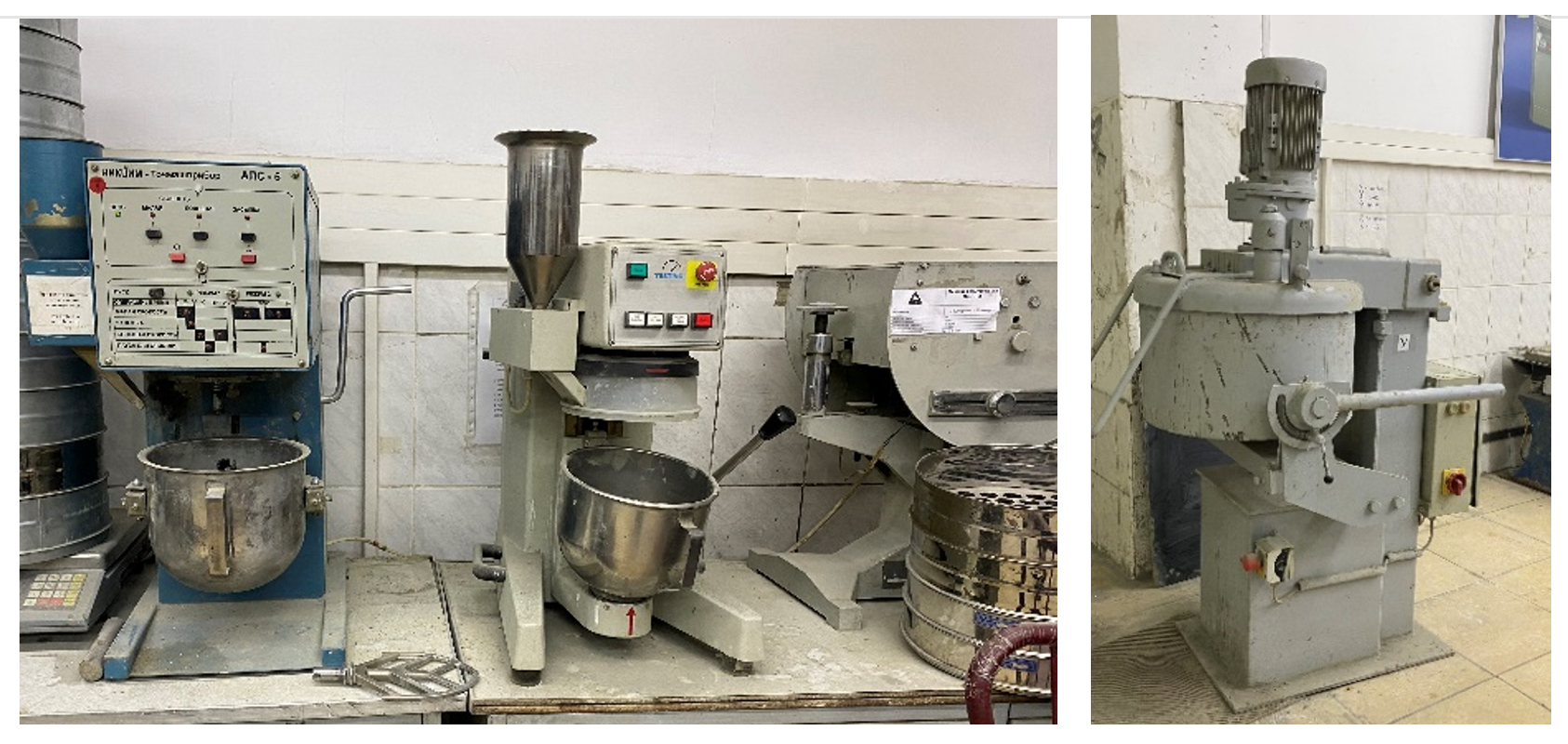
Рисунок 2 - Смесители германской фирмы «TESTING» емкостью 2 и 50 л, российской фирмы «НИКЦИМ Точмашприбор АЛС-5» емкостью 3 л
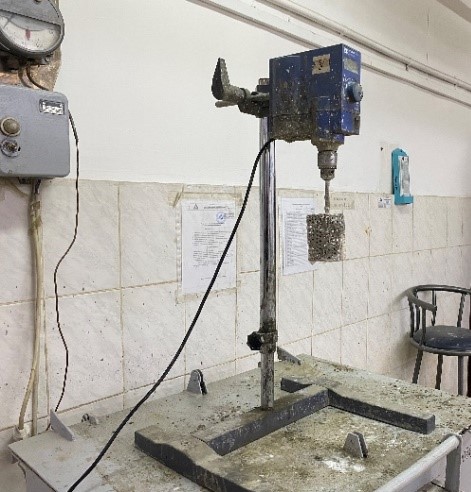
Рисунок 3 - Аппарат для получения пены
3. Основные результаты
В соответствии с требованиями ГОСТ 10832-2009 (Песок и щебень перлитовые вспученные) (п. 5.1.2), для приготовления легких бетонов необходимо применять вспученный песок рядовой, т.е. марки ВПР, в котором содержатся зерна размером от 0,16 до 5,0 мм, а содержание зерен размером менее 0,16 мм должно быть не более 10 %. Песок же, вырабатываемый на предприятии Заказчика (табл. 3), состоит из очень мелких зерен. Так, в них диаметр основного объема зерен (86,6% без учета пылевидной части) не превышает 0,6 мм, а с учетом зерен менее 0,16 мм – 89,9%. Таким образом, можно констатировать, что вспученный из Арагацкого месторождения перлитовый песок не соответствует ни одной группе по зерновому составу регламентируемого вышеуказанным стандартом.
Специфика зерен вспученного перлитового песка, заключающаяся в хрупкости, ломкости, низкой прочности не позволяют перенести способы приготовления легких бетонов на основе других пористых заполнителей (керамзита, аглопорита и др.) на технологию перлитоцементной массы. И есть второй, не менее важный отличительный фактор: для их приготовления расходуется слишком мало цемента, что обуславливает трудность получения однородной массы. Например, в первом приближении, при проектировании состава перлитоцемента плотностью 200 кг/м3, объем перлитовых зерен на 1 м3 смеси составит 1200-1400 л, а объем цемента всего – 32-36 л, т.е. объемы исходных материалов отличаются на два порядка.
По известной технологии вначале готовится цементная шликерная масса с большим избытком воды, затем в смеситель вводят вспученный перлитовый песок и производят перемешивание . С цементом шликерную массу можно получить только в том случае, если в состав смеси ввести компонент с высокой водоудерживающей способностью, в качестве которого при получении перлитоцементных изделий используют распушенный асбест. Нами, вместо асбеста, применяется пена, что позволило резко сократить количество вводимой воды.
Для получения конкурентоспособных плит необходимо разработать состав перлитоцемента с максимально возможно низкой плотностью, что обеспечит наименьший коэффициент теплопроводности. Согласно ГОСТ 25820-2021 (Бетоны легкие), по средней плотности в сухом состоянии теплоизоляционные бетоны подразделяют на марки: D200, D250, D300, D350, D400, D450, D500 при прочности на сжатие от М2 до М25 и коэффициенте теплопроводности от 0,07 до 0,14 Вт/(м·°С) в сухом состоянии. В примечании к п. 5.4.5 указывается, что для теплоизоляционных плит прочность на сжатие характеризуется марками М3, М10, М15, М25, М35, М50, М75, М100. Отсюда следует, что независимо от плотности перлитоцемента, его минимальная прочность должна быть не менее 0,3 МПа.
С учетом предписаний стандарта эксперименты проводились по получению перлитоцемента марки D200, т.е. минимально допустимой марки по ГОСТ 25820-2021. При проектировании состава перлитоцемента исходили из того, что основными компонентами, влияющими на плотность, являются вспученный перлитовый песок и цемент. Функциональные добавки, вводимые в состав смеси, на плотность материала оказывают незначительное влияние.
Регулируя соотношение «вспученный перлитовый песок-цемент» были получены образцы с плотностью в сухом состоянии 150-200 кг/м3. Испытание на прочность после 28 суток выдерживания в нормальных температурно-влажностных условиях показало, что прочность образцов на сжатие находится в пределах 0,09-0,15 МПа, что недостаточно как для легких бетонов (требуется минимум М2), так и для теплоизоляционных плит (минимум М3).
Введением функциональных добавок, включающих ускорители схватывания и твердения цемента, адгезионные и когезионные свойства, а также межзерновой пористости заполнителя, регулированием расхода пены и его плотности, прочность образцов после 28 суток твердения составила 0,32-0,43 МПа, что удовлетворяет требованиям стандарта. При этом расход хлористого кальция составил 3%, а жидкого стекла – 2,5% от массы цемента.
Таблица 4 - Зависимость между прочностью на сжатие и соотношением «цемент/перлит»
№ состава | Расход компонентов на 1,5 л бетона | Показатели бетона | |||||
цемент, кг | перлит, л | вода, л | пена, л | плотность в сухом состоянии, кг/м3 | прочность на сжатие через 28 суток, МПа | коэффициент теплопроводности, Вт/(м·°С) | |
1 | 168 | 1,5 | 0,4 | 1,5 | 210 | 0,05 | 0,052 |
2 | 150 | 1,8 | 0,45 | 1,5 | 205 | 0,07 | 0,051 |
3 | 132 | 2,1 | 0,5 | 1,5 | 200 | 0,09 | 0,048 |
4 | 113 | 2,4 | 0,6 | 1,5 | 205 | 0,12 | 0,048 |
5 | 100 | 2,7 | 0,7 | 1,5 | 195 | 0,15 | 0,052 |
6 | 77 | 3,0 | 0,8 | 1,5 | 200 | 0,13 | 0,051 |
7 | 60 | 3,3 | 0,85 | 1,5 | 200 | 0,10 | 0,050 |
На рис. 4 представлены макро- и микроструктура перлитоцементных образцов, из которых видно, что зерна вспученного перлитового песка состоят из тонкостенных полусфер различной формы. Этим и объясняется низкая прочность и хрупкость перлитового песка.
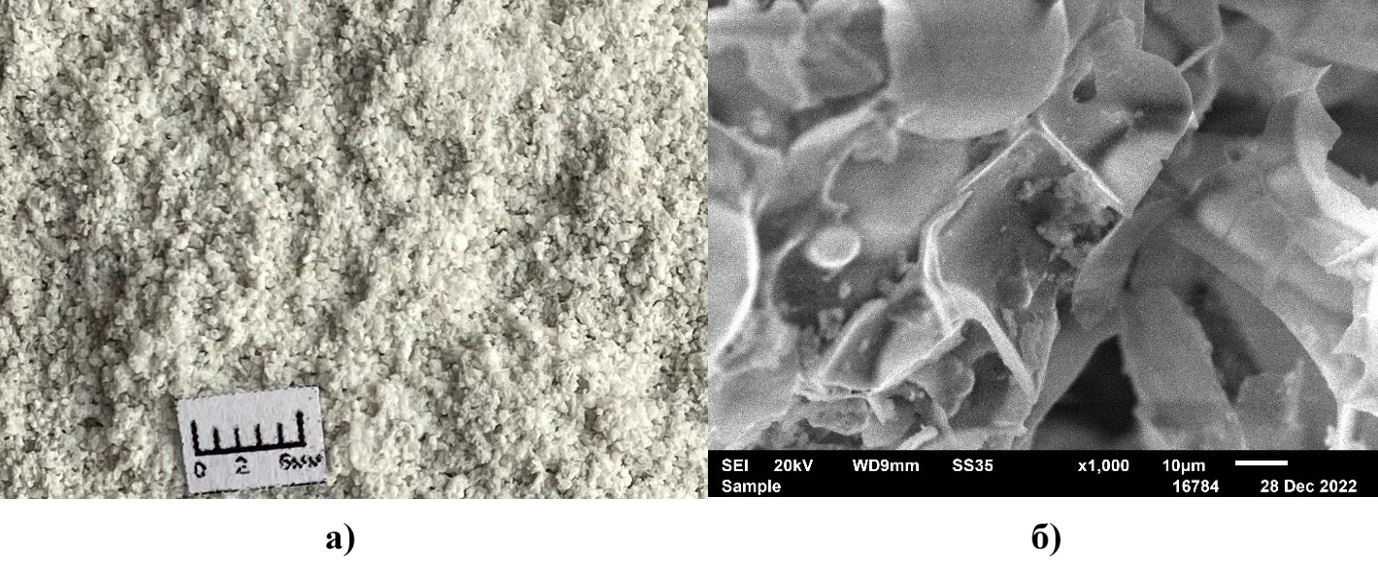
Рисунок 4 - Макро- (а) и микроструктура (б) перлитоцемента плотностью 200 кг/м3
4. Заключение
В результате экспериментальных исследований получен особо легкий перлитоцемент, для изготовления которого вместо подготовки асбестоцементного шликера готовится пеноцементная масса, которая перемешивается со вспученным перлитовым песком. Плотность перлитоцемента 150-200 кг/м3, прочность при сжатии 0,32-0,43 МПа, коэффициент теплопроводности – 0,048-0,052 Вт/(м·°С). Плиты на основе особо легкого перлитоцемента рекомендуются для тепловой изоляции наружных стеновых конструкций жилых и общественных зданий.